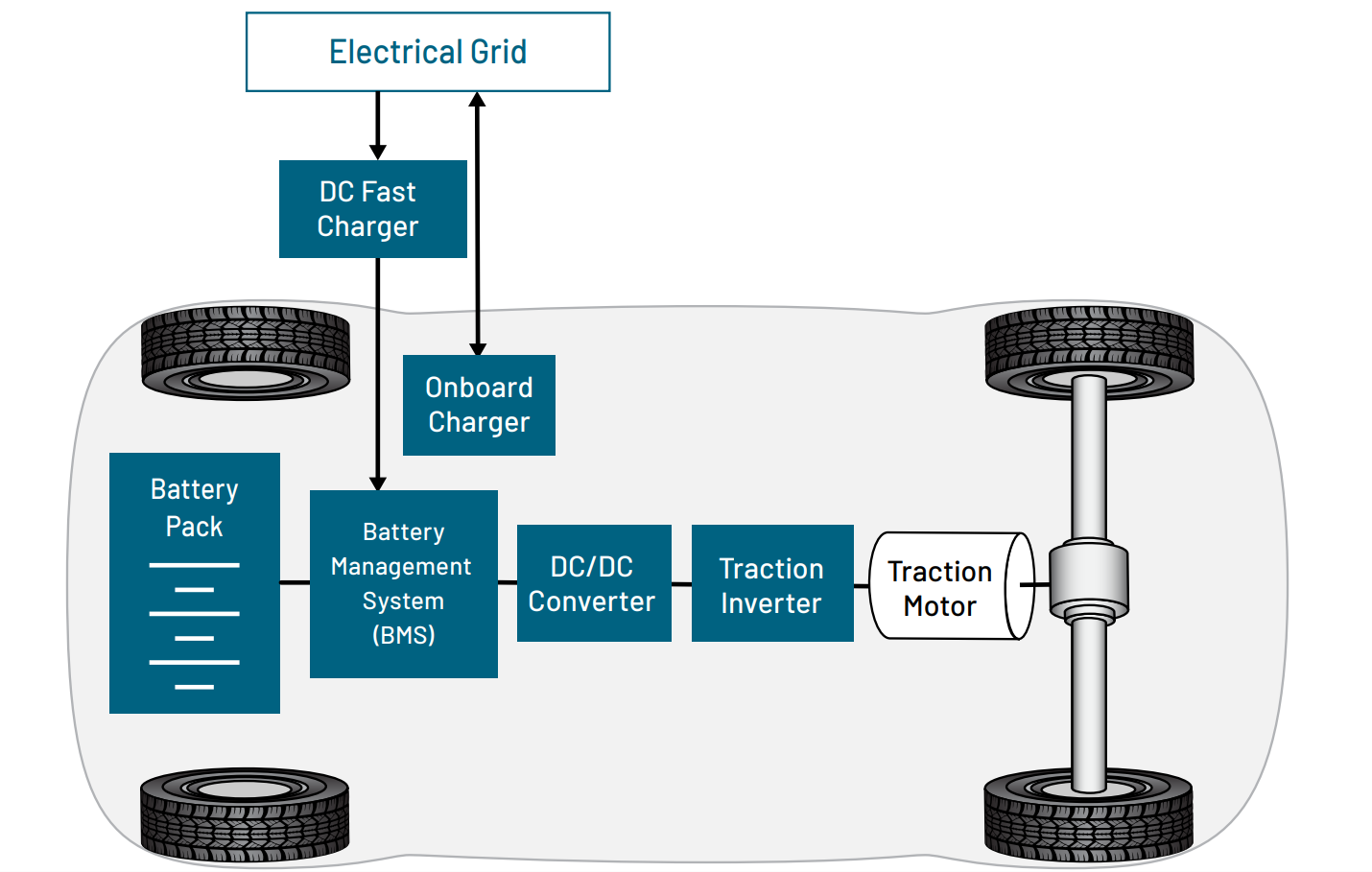
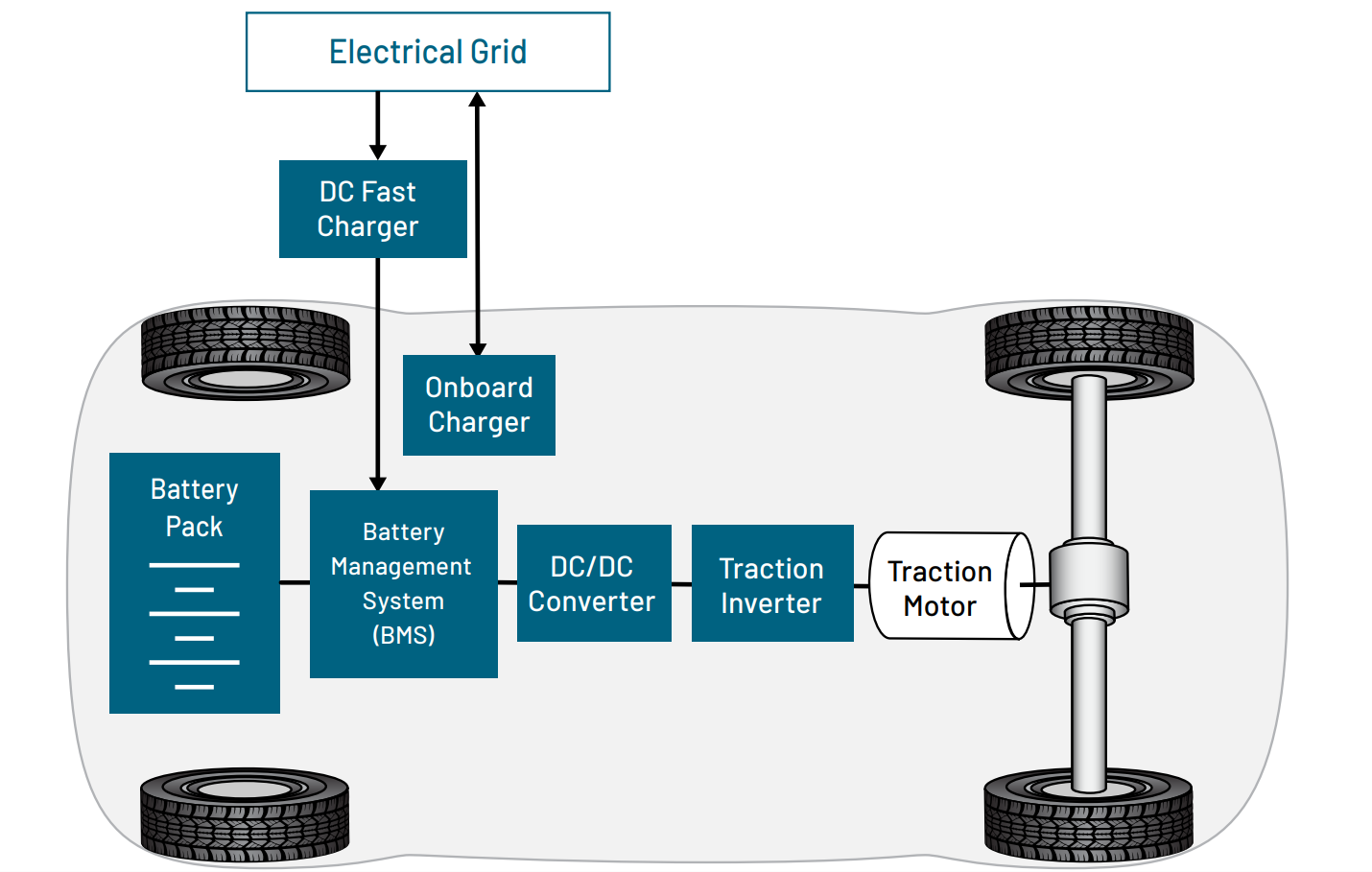
The rise in the adoption of electric vehicles (EVs) is leading to new test challenges to optimize the designs, reduce costs, and make the vehicles more efficient. The various power converters and traction inverters form the heart of the EV powertrain subsystem and are one of the critical blocks that need to be tested to achieve the highest efficiency. Wide bandgap technology like SiC/GaN are positively supporting these efforts, but at the same time have their own test challenges that need to be addressed.
The introduction of the 800V powertrain architecture marks a significant leap forward. Let’s take a look at the design and test challenges associated with 800V powertrain architecture for Electric Vehicles.
Unlocking Potential with 800V Systems
The 800V powertrain architecture refers to the electrical system in an EV (usually electric trucks and construction vehicles) that operates at a nominal voltage of 800 volts. This is a significant increase from the more common 400V powertrain architecture used in battery electric vehicles (BEVs) today. These require recharging times of 40 to 120 minutes on a public DC fast charger (DCFC). These timeframes are constrained by the practical cable size needed for transporting the required current to the battery pack. 800V BEVs are a promising alternative, to reach ultrahigh charge rates of 350 or 400 kilowatts.
The transition to 800-volt architecture-based BEVs offers a solution to mileage, or “range anxiety.” Doubling the voltage while maintaining the same current results in doubling the energy input to the vehicle. With the ability to recharge your vehicle 50 percent faster (in other words 50 percent reduction in charging times), this advancement significantly diminishes concerns about depleting the battery during extended journeys.
Bar chart of 800V system production share growth from 2020-2030. Source: Yole market research
Increasing Range of BEV
As a result, these vehicles exhibit the potential to charge from 5 percent to 80 percent state of charge, which equates to roughly 200 miles of range, in under 23 minutes. This stands in stark contrast to the 40 to 120 minutes typically associated with 400V battery powertrain systems available today.
Moreover, the elevated voltage allows the same power to be delivered with lower current, enabling the utilization of smaller diameter cables and connectors within the powertrain. leading to a lighter electric vehicle, and ultimately longer driving range for a comparable battery pack.
Other benefits of transitioning from 400 to 800 volts include improvement in overall efficiency and easier thermal management across the powertrain subsystem.
According to market research agency Yole, they are anticipating that in 2023, the automotive industry will begin to embrace 800V systems as a mainstream solution. This shift is driven by the numerous advantages mentioned earlier, particularly in premium vehicle segments, with automakers like Audi, Porsche, Hyundai, and Kia leading the way in early commercialization. While only a small handful of public DCFC stations can currently take full advantage of the 800V architecture today, that number is increasing daily, and we are probably not that far away from the majority of public DCFC stations being 150 kW or higher within the next 5 years.
Temperature Benefits of Wide Bandgap Devices
Regarding hardware approaches, the emphasis is on employing wide bandgap (WBG) semiconductors like SiC and GaN switches. This choice is due to their rapid switching capabilities and elevated temperature tolerance. These components function effectively at elevated temperatures, resulting in improved efficiency and reduced Total Harmonic Distortion (THD). The extended operational temperature range of wide-bandgap devices can also simplify inverter design and minimize the necessity for thermal management systems. In our collaboration with standardization organizations such as JEDEC and IEC, we concentrate on standards related to switching analysis and diode reverse recovery measurements, which are pivotal for characterizing the performance of wide-bandgap devices.
Oscilloscopes Play a Crucial Validation Role
Oscilloscopes play a crucial role in validating and diagnosing issues with EV traction motors and inverter designs. They empower designers to meet ambitious efficiency targets. However, it's essential to recognize that an oscilloscope alone may not be sufficient for all these measurements.
Probing solutions and analysis software play key roles. Optically isolated voltage probes help designers make measurements on high-voltage gate drive
Tektronix offers a wide bandgap double pulse testing (DPT), or double pulse test, solution on 4 Series B MSO, 5 Series B MSO and 6 Series B MSO oscilloscopes – that help engineers achieve accurate, repeatable measurements on state-of-the art power converter designs.
Specially tailored software, such as Tektronix's IMDA (Inverter Motor Drive Analysis) offering, complements these capabilities by enabling three-phase measurements for PWM and mechanical data, enhancing the overall utility of the solution.
To measure the appropriate magnitudes and frequencies at crucial junctures, dedicated current and voltage probes are indispensable. The 5 and 6 Series MSO oscilloscopes serve as an excellent solution for engineers engaged in EV powertrain designs, offering a high-channel count, inverter analysis software, and versatile probing options.
Tektronix engineer performing electric vehicle power train testing with a 5 Series B Oscilloscope.